Applied Materials Announces New Tool and Architecture for Next Generation OLED Manufacturing, Samsung Display Now Assessing Their Technology
OLEDs found in smartphones, tablets, laptops, smartwatches and automotive applications are fabricated using a fine metal mask vacuum thermal evaporation (FMM VTE) tool. While Applied hasn’t disclosed pricing for their solution, FMM VTE tools can cost $500M each at G8.7 for 7.5K capacity for a tandem stack and the total FMM VTE expenditure for a 15K substrate per month tandem OLED fab can reach $1B. Equipment suppliers can only make and install a couple of these giant tools per year which can easily fill a football field, constraining the pace at which OLED manufacturers can build and expand capacity targeting future applications. In addition, the FMMs constrain OLED performance and limit the maximum size that can be produced. The ultra-thin fine metal masks are inherently constrained by sag, geometrical distortion and the tapered hole shape which results in a smaller OLED pixel and aperture ratio than if they were patterned by lithography. As the FMMs grow, the problem gets worse. With panel manufacturers looking to use larger substrates and build larger panels, FMMs can compromise this effort. In addition, the FMMs themselves are also expensive, take a long time to manufacture, need to be cleaned regularly, can lead to cross contamination impacting yields and require very precise positioning which impacts tool costs and can impact yields.
Please register or login to read full article
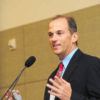